A cheese manufacturer developed in-house automation capabilities to keep legacy equipment running and responsively adjust to production demands.
Many companies rely on external firms for automation upgrades and changes, and this works well for countless applications. But Pacific Cheese Company faced a dual challenge of maintaining and improving manual and legacy systems, while at the same time upgrading operations to responsively meet changing consumer demands. Michael Blackstone, a project manager for Pacific Cheese Company, describes in a Design World July 2023 article titled Automation Upgrades Keep Cheese Manufacturer Sharp how he and his team were able to develop automation skills within the company to best deliver and support the solutions they needed.
Controlling Big Cheese Operations
As a converter and packager of cheese for major retailers and foodservice customers, Pacific Cheese operates a variety of equipment to create blocks of cheese and packaging pouches with specific requirements and labelling, with maximum uptime and flexibility key to success.
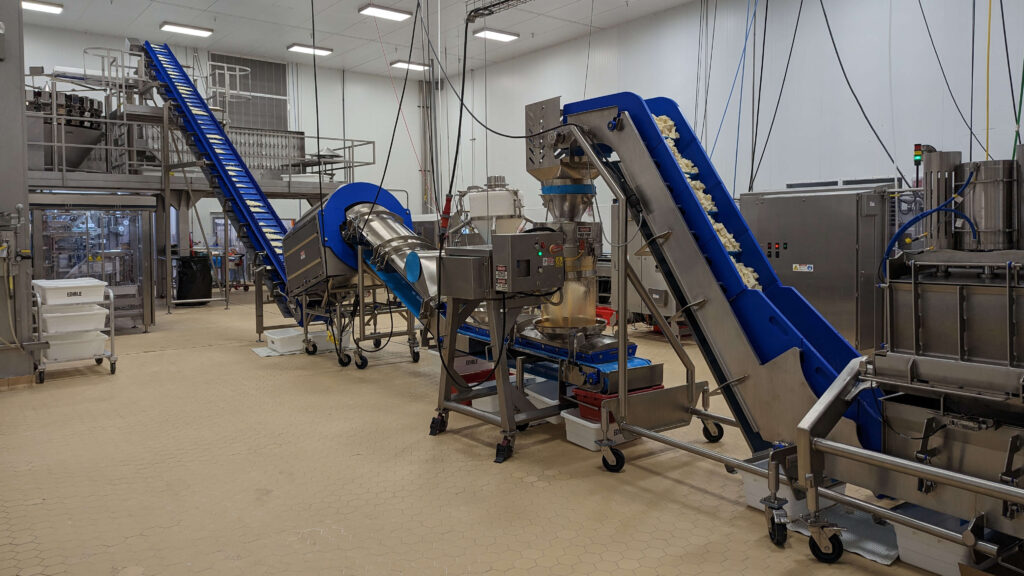
However, the existing systems were largely manual and hardwired, even though some equipment came with legacy PLCs. There was no HMI, the machinery was sometimes poorly coordinated upstream/downstream, and stoppages happened frequently, often for no apparent reason. Product changeovers required significant effort and adjustment.
As new equipment and an entire production line were added, it was clear that updated automation would be needed to fully realize throughput and production capabilities. The team knew how the equipment should run, but they needed a suitable automation platform to make it happen, so they first used a single pilot project to test-drive an automation platform. After evaluating the following criteria, they zeroed in on AutomationDirect due to its:
- Price: Hardware costs are less than “leading brands,” but experience has proven the quality to be excellent.
- Support: The team rarely needed help, but they found that free online support—such as website information, manuals, and forums—and also phone support, quickly resolved any issue.
- Products: The team could order all PLC and HMI devices—as well as associated components like sensors, relays, safety devices, power supplies, and more—right from the website.
- Software: Free and low-cost software that is easy to use was perhaps the number one reason for satisfaction with the AutomationDirect product platform.
The team generally standardized on Productivity1000 stackable micro PLCs, combined with C-more HMIs, both of which are compact and easily retrofitted into existing cabinets.
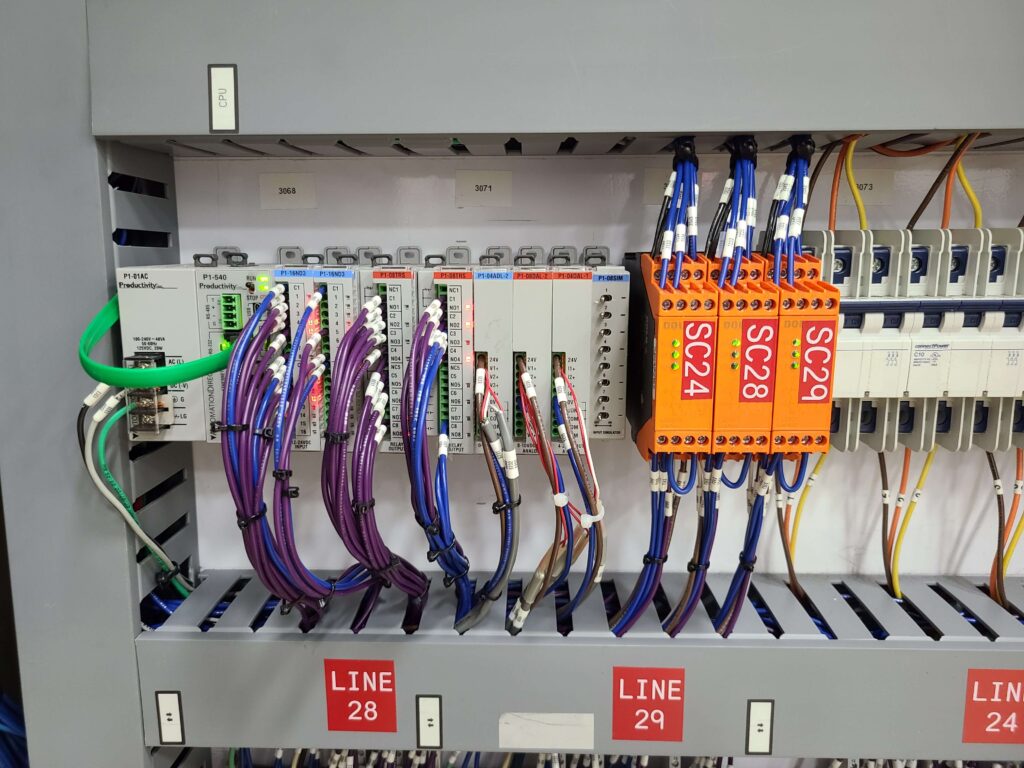
Additional Upgrade Benefits
Superseding existing functionality was a baseline goal, but the team really wanted to raise the bar on automatic operations, flexibility, and usability. They did so by:
- Creating useful HMI graphics
- Adding clear operations and warning messages
- Developing a specific sanitation mode with countdown timer, which runs the equipment slowly for good cleaning, and then stops the cycle at the right time to save energy
Although the team had to tackle a learning curve to design and program their own systems, they have now executed many successful and valuable projects using this approach.
Now they control their own destiny regarding legacy automation upgrades, and their in-house programming capability lets them improve operations in dozens of ways based on what their team and operators know, learn, and need.
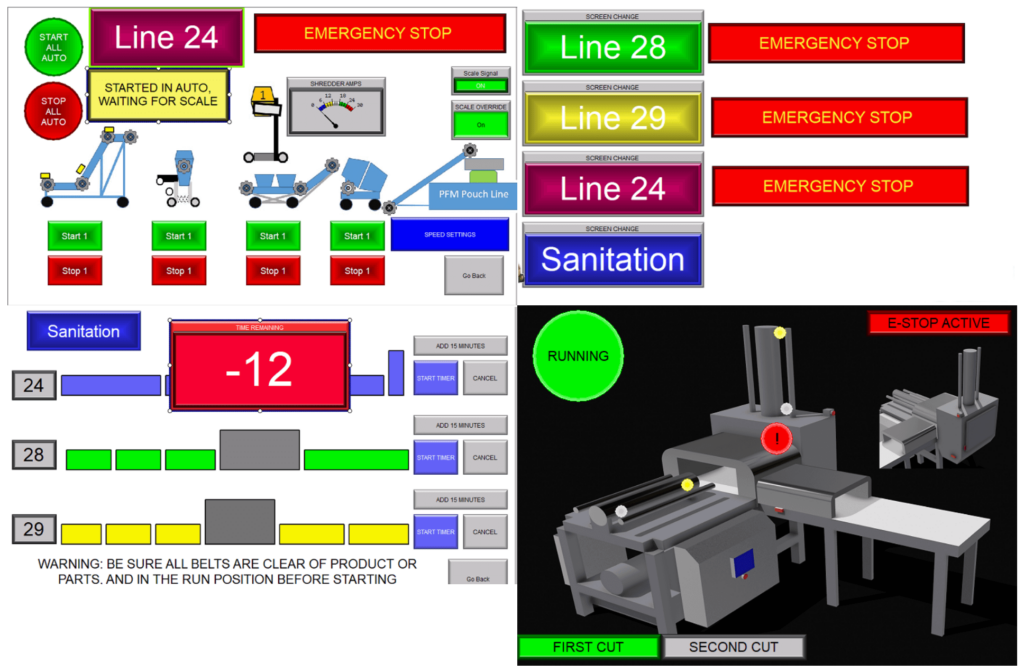
Check out the AutomationDirect.com website today to explore products that can help your company control its own automation destiny.
All figures courtesy of Pacific Cheese Company